groundloop
Active member
After that, I used a rubber mallot, chisel, (wide) pry-bar, piece of thin alum plate and 1x that I cut into wedges and slowly worked them down being careful not to penetrate the outer skin. I worked the chisel (approx 1") on the top busting out the bondo/concrete stuff and then used it to pry between the outer skin and wood. Once started, I just worked back and forth going deeper and deeper until it gave way.
Well, I started out trying that method and it didn't work out too well. My transom was very wet throughout, but still had good adhesion to the fiberglass skin. The instant I started to tap a pry bar or wood chisel between the plywood and skin, the skin bulged out and some hairline cracks formed in the gelcoat. Since the gelcoat is in pretty good condition I wanted to avoid doing anything to screw it up, so abandoned this method in favor of my good friend Mr. Wood Chisel. It took about 5 hours to get all the wood chipped out. (I imagine I'd have had better luck with this if the transom had been more rotted and delaminated from the rear skin). I did manage to get the fiberglass off the forward face in one piece so that I'll be able to use it as a template.
Here's my very wet transom (which is HEAVY!!!) :
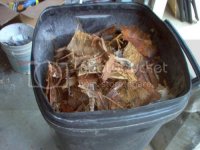
and here's the rear skin after grinding off all remnants of plywood and filler:
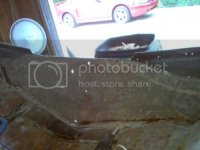
I also found that most of the wood in the box structures under the gunwales (anyone know the proper name for them?) is wet and rotting, so those are coming out as well.
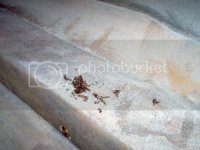
Being an engineer, I like to try and understand why things are built the way that they are. These boxes have a sheet of stiff foam (approx. 1/8" thick) between them and the side of the hull, and are constructed like this:
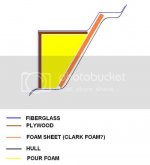
The part I understand is that by using the foam sheet between the box and hull, and allowing it to "float" without being bonded to the hull, there is a small amount of flex built into the side of the hull. The part I haven't figured out or had explained to me yet is why is is it desireable to build flex into the sides like that. If anyone can explain this please speak up.
It would be easier (and cheaper) to rebuild these without that sheet of foam, but I'll probably include it to stay close to the original design's intent. If anyone else has to rebuild these in the future that foam is pretty close to what used to be called Clark foam, and is now available under the name "Last-A-Foam" from Wicks Aircraft or Aircraft Spruce (in the past I've had better service from Wicks Aircraft and prefer to use them whenever I have a choice).